EMBARRASSING EXAMPLES
Gleaned from actual projects, the following examples communicate very clearly to roofing contractors that the designers have:
- Very little knowledge in what they have specified and/or drawn.
- Will not be able or don’t care to check the submittals or work in the field.
- No inclination to be on the roof to observe the construction. The contractors can pull the wool over the architects’ eyes.
Figure 1, below, had no specification, just a cut sheet for the membrane.
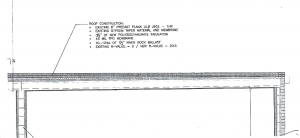
Figure 1: This detail had no specification, just a cut sheet for the membrane.
The contractor took multiple test cuts and found two roofs: aggregate-surfaced four-ply BUR on a 2-inch lightweight pour over EPS on a four-ply smooth BUR on perlite mopped to precast deck. If you read the detail, it calls for a ballasted TPO, a system most manufacturers will not warrant.
Figure 2 is actually a detail put out by a consultant.

Figure 2: This is a great detail at 10 percent completion.
It’s a great detail at 10 percent completion! You can see it is totally inadequate and does require some structural engineering. The consultant adds insult to injury by requiring the contractor to install perimeter sheet metal and provide a letter from the manufacturer in the bid that the sheet metal com- plies with a 20-year warranty requirement. However, there is no mention of code-required ANSI/SPRI ES-1 compliance. And somebody is paying for this crap?!
The “An Actual—and Poor—Scope of Work” sidebar, page 4, was issued by an architect. The scope is for a re-cover, but test cuts revealed phenolic insulation on steel deck! No manufacturer will warrant a roof going over phenolic foam insulation. No consultant or architect with a fifth-grade education would specify going over phenolic.
HOW YOU CAN IMPROVE
I want to bring to the attention of members of the design community that they are treading on violations of their standard of care. Should any of their roof designs end up in litigation, guys like me will have a field day with what has been produced. Consider this a wake-up call! I now will provide some suggestions and recommendations to the previously noted concerns:
A. THE ROOF SYSTEM DESIGN IS NOT CODE COMPLIANT IN REGARD TO TAPERED INSULATION.
The 2015 code now requires that the ASHRAE Zone-required insulation thermal value be achieved within 4 feet of the center of the roof drain. No longer can you use an average thickness as a gauge. For Chicago, that means R-30, or 5 1/2 inches of polyisocyanurate, equally at 4-feet out from the drain. This will impact the roof edge, roof drain (now you will need to detail extension rings), access doors and penetrations. (See Roofing’s September/ October 2016 issue, page 58.)
B. THE ROOF SYSTEM ITSELF IS NOT CODE COMPLIANT, BUT CONTRACT DOCUMENTS REQUIRE “CONTRACTOR TO VERIFY OR BE RESPONSIBLE FOR CODE COMPLIANCE”.
It doesn’t take much to design a roof to be code compliant. Designing one that is not code compliant is a travesty. Asking the roofing contractor to verify and be responsible for code compliance is well below the standard of care for a licensed design professional being remunerated for a roof system design that is code compliant. Read the appropriate code sections, review with code officials and all manufacturer technical representatives, ensuring your design meets the local code. Then, consider this: Exceed that code for the benefit of your client.
C. STRUCTURAL AND, ESPECIALLY, STRUCTURAL LIGHTWEIGHT CONCRETE POSE SIGNIFICANT ROOFING CHALLENGES AND ARCHITECTS HAVE NO CLUE ABOUT THAT, RESULTING IN ROOF SYSTEMS IN DANGER OF IMMINENT FAILURE.
The biggest issue in the roofing industry is concrete roof decks and the moisture they release. You need to understand that moisture and roofing do not mix. Moisture migration from concrete into roof systems is a design issue not a warranty item. Normal structural con- crete will take more than 60 days to dry; with lightweight structural concrete, you are looking at more than 180 days before roofing should be applied. Bet you didn’t know that! When you consider re-wetting, that time could be longer. If your designs utilize cast-in- place concrete, you really need to think about your roof system design. Consider vapor retarders and ballasted systems. If you want to go fully adhered, consider a vapor retarder and mechanical fastening of the insulation (at least the first layer). Litigation regarding cast-in-place concrete is at an all-time high.
D. THE ACCURACY OF CONSTRUCTION DOCUMENTS IN GENERAL IS VERY, VERY LOW. EVEN I CANNOT OFTEN DETERMINE WHAT ROOF ASSEMBLY AN ARCHITECT WANTS FROM A SPECIFICATION.
It is stunning how many specifications I read that don’t indicate what the roof system is until the membrane applications section in Part 3. This is wrong! Make the roof system type immediately clear in the “this section involves” part of the specification. List all the components of the roof system and their application method. For example:
- 1. Substrate board mechanically fastened at 1/2 square foot with self-adhering vapor retarder on primer surfaces.
- 2. Two layers of 2.6 rigid 25 psi, double-coated fiberglass faced ISO set in bead-foam adhesive at 4 inches on-center.
- 3. Cover board set in bead-foam adhesive at 4 inches on-center.
- 4. 90-mil fully adhered EPDM.
- 5. 2- by 2-foot by 2-inch rubber walkway pads.
Additionally, too many specifications used are generic with out-of-date materials and/or manufacturers. I even see specifications that are not for the details drawn, like a BUR specification with a detail for a single-ply roof. Don’t look so duncical!
Drawings and details should be project-specific, cover all conditions and be explicit. By the way, manufacturers provide details as a basis for your designs, not as the design in itself.
The specification and drawings should complement each other. If you have an EPDM roof, you should have noted this on the details and specified it in the spec. No other roof material should be in the specification. Do not bid alternative membranes without a second set of details explicit for the other system. I know you want to do this, but resist the temptation as nine times out of 10 it comes back to bite you in the form of change orders and/ or as an error or omission.
Illustrations: courtesy of Hutchinson Design Group Ltd.
Well said and written Tom. I would like to meet sometime when I come to Chicago. I will be there in April if you have the time.
Christopher Gentile RRO
586-855-0687